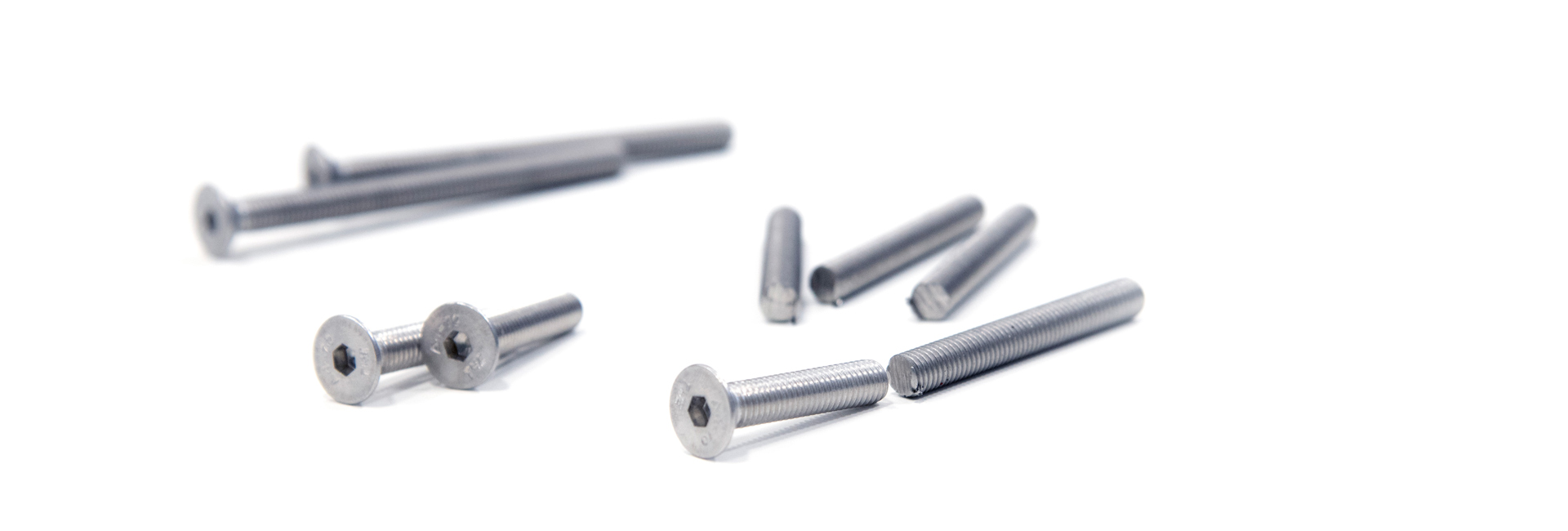
Mechanical machining of screws – Bespoke adaptation
Standardized connecting elements often come very close to the screw you want, but one or more details do not quite match. Mechanical machining then creates a perfect connecting element out of the screw that is almost right. Targeted modification during mechanical machining of the screw can be used to adapt the connecting element to the installation scenario or the desired appearance. For example, screws that protrude because the thread is too long are often not wanted. Cutting them to the optimum level fixes the problem. Screws used at positions that are relevant to safety often have to be secured against unintentionally coming loose. Mechanical machining of the screw can provide this safety feature.
The entire screw can be machined, including the screw drive, the head shape or the screw thread. You tell us what changes you would like to a screw and we take care of the rest. Precise mechanical machining of screws allows many changes to be made.
Mechanical machining of screws according to requirement
Below you will find typical form of mechanical screw machining that customers repeatedly order from us:
• Changing from threaded rods to anchor rods
• Reducing the head diameter of the screw to the size required
• Removing or changing the stamp on the screw
• Creating an undercut in the desired shape
• Re-working the screw for thinness
• Inserting cotter pin holes and other locks to prevent loosening or rotation
• Extending threads
• Changing the thread to a fine thread
• Changing the thread to a left-hand thread
All key procedures can be performed
All common methods of mechanical production can be used for mechanically machining screws. The starting point is provided by screws from the standard ISO or DIN families. You then define the desired changes.
If a change to a standard screw does not lead to the desired result, then the solution can be delivered in the form of a special or custom part. Otherwise, mechanical machining represents the easiest solution for adapting screws to the job at hand.
The following methods are available
for the mechanical machining of screws:
Sawing. Sawing is the normal procedure used for cutting screws. Similarly, threaded rods can be shortened by sawing or dividing them into several sections.
Turning. Turning is used to perform all rotationally symmetric forms of machining. These include the production of undercuts and turning thin shafts. The head diameter of a screw can also be reduced on the lathe, provided that the screw drive is on top of the head. Turning is also used to remove any unwanted stamps from the screw head.
Threading and thread machining. To furnish the screw with a thread extension and to produce fine threads and left-hand threads, a new thread is rolled on using rolling dies. This makes it much harder and more resilient than a cut thread.
Milling. Milling is used on screws to produce external hexagon and external square screw heads.
Hexagon screws are additionally furnished with a milled screw slot in order to prove more attachment options.
Drilling. Drills are used to make cotter pin holes and head holes.
Do you have any questions?
Do you have any test certificate, special packaging or special packing needs?
Our sales team will be more than glad to help you and inform you about the many options we have available for surface coating, thread locking and head painting.
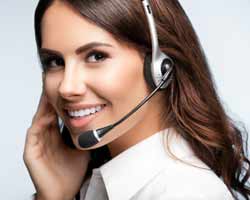
Our Sales Team will be more than happy to help you further:
T: +49 7941 6073-0 sales@tobsteel.com